Operational Intelligence Flows from Dispenser Filters
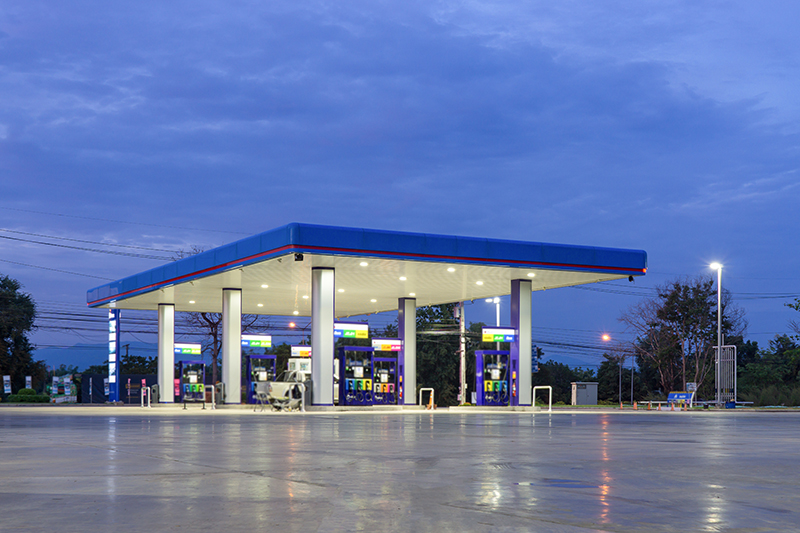
Hey, fuel site operators and technicians: Your site’s dispenser filters might be trying to tell you something important. Are you listening?
Keeping a fueling system in sound working order takes as much awareness and stamina as it does expertise and technical aptitude. Perhaps surprisingly, a relatively inexpensive part of a fueling system – the dispenser filter – can help signal operators to critical operational weaknesses that, if left unchecked, could erode a fuel site’s bottom line.
If dispenser filters could talk, here are three things they would tell you:
1. If the dispenser’s flow is slow, act fast to minimize costly consequences.
Dispenser filters cue operators into deteriorating product quality and/or infrastructure problems by disrupting the flow of fuel in the following ways:
- As the filter collects particulate, flow becomes restrained. If this happens earlier than planned maintenance intervals, then it is likely an indication of a problem with the fuel, storage and dispensing equipment, or both.
- If fuel that has completed phase separation passes through the filter, a specially treated polymer inside the filter expands and congeals, increasing the total differential pressure, which significantly slows the flow of the fuel.
- Similarly, if the filter senses water, the filter reduces the flow.
2. Perform a “filter autopsy” to get the real dirt on the health of your fueling system.
A used dispenser filter offers a snapshot of the quality of the fuel recently pumped through the dispenser as well as an indication of the conditions inside the tank. By examining the contents of a used dispenser filter, operators and technicians can obtain insights to the factors contributing to deficiencies in fuel quality.
3. Learn how to “read” a used dispenser filter.
Familiarize yourself with these signs of fuel contamination or tank corrosion that may be observed during day-to-day operations or during a visual inspection of a used dispenser filter:
- Flow becomes restricted prior to planned maintenance intervals due to a clogged dispenser filter
- Corrosion of interior metal filter parts
- Particulate in the filter – solid or semi-solid contaminants that resemble a reddish-orange metal and/or scaly, granular deposits
- Microbial slime in the filter
- Foul odor that smells like rotten eggs
- Extreme discoloration/leopard spotting
In market research conducted by PetroClear, 52% of customers surveyed indicated that slow pumps are the primary motivation for changing their dispenser filters. While providing a positive customer experience is absolutely important to long-term successful operations, so is staying on top of infrastructure maintenance. Following a regular filter maintenance program is not only the best practice for maintaining high fuel quality standards, but it offers operators an opportunity to observe signs of “bigger picture” issues in the fueling system and proactively get corrective measures in motion.